Discover which systems need work and how to justify expenses.
by William Livoti
The term system optimization is widely known, but how many people truly understand what it means? Total system efficiency has been a real challenge for the industrial sector to embrace.
Lack of Standards Hinders Configuration
Except for a few standards for package boilers, there are no system standards. What does this mean, and how does this impact your plant bottom line? Anyone can design, configure and specify a pumping system, but no one can say it is incorrect without a system standard (ASME, ISO, ANSI, HI). In my 45+ years in the pump industry, I can count on one hand the number of pump systems that were properly configured.
Given the focus on energy efficiency and sustainable growth in today’s industry, system optimization should be addressed in every pump system specification in some way, shape or form. The Hydraulic Institute defines system
optimization as:
The process of identifying, understanding and cost effectively eliminating unnecessary losses while reducing energy consumption and improving reliability in pumping systems, which while meeting process requirements, minimizes the cost of ownership over the economic life of the pumping systems.
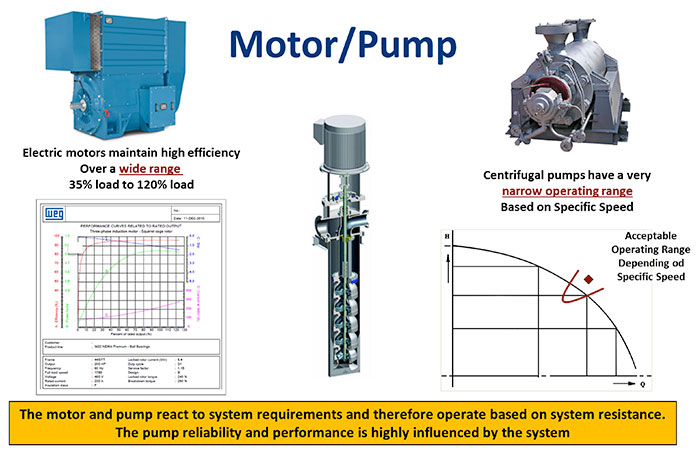
Figure 1. The motor and pump react to system requirements and operate on system resistance. (Graphics courtesy of the author)
Why Focus on Pumping Systems?
A pumping system’s efficiency is highly influenced by the system it is supplying; therefore improving pump or motor efficiency will do little to reduce pump energy use. The focus must be on the entire system because the motor and pump react to the system (see Figure 1).
The motor has a wide operating range maintaining high efficiency to as little as 50 percent load. The pump has a rather narrow operating range (depending on specific speed) and will lose efficiency quickly.